From ‘shrimp leather’ to synthetic dye, are biomaterials finally ready to scale up?
Seymourpowell’s Caroline Jacob on the power of biotech and how it can transform materials.
Biofabrication has been selling the promise of a harmless, resilient, and versatile alternative to traditional materials for nearly a decade, and yet the industry has never truly scaled. Efforts are often stymied by complex, labor-intensive, and expensive processes.
However, after at the 10th anniversary of the Biofabricate Summit earlier this year (the densest gathering of bio innovators in the world) it seems that biotech has finally reached maturity. Innovative companies are increasingly ushering in new technologies—signaling a seismic shift that’s set to unfold a whole new category of high-quality, low-impact materials that are naturally produced, of known provenance, and made-to-order.

What can we learn from the most successful companies in the field? And most importantly, how can we deliver biomaterials that truly work?
A subsection of bio-based materials, biofabricated materials utilize living organisms (such as microbes) rather than plants or animals. Their appeal and power are therefore found in their low-impact and regenerative qualities. The advent of these biomaterials signals that greater infrastructures are now in place to make consumer adoption and global scalability an economic reality. Today, green technologies have more investment, raw components for biomaterials are more abundant, and automation is optimizing manufacturing. Additionally (and crucially!) consumers are no longer viewing the product as a poor cousin of more traditional materials.
As someone who certifies materials on the daily, here are my thoughts on the power of biotech and its potential implications on how we make, create, and consume for the better.
Unleashing the new fabric of creativity
One of the most exciting things about biofabrication is that new functionalities and aesthetics can be engineered at the conception stage to create customizable materials that can outperform their pollutive forerunners.
Think about biomaterials composed of by-products, like sawdust, which can be crafted to match the butter-soft textures of real animal-derived leather; or biological dyes that encompass the vibrancy of their synthetic counterparts but are devoid of toxic chemicals. These aren’t pie-in-the-sky ideas, but real material innovations that are set to impact everything consumers interact with: from the new clothes on our backs to the carrier bags we use at the point of purchase.

Take U.S. startup TômTex, with its biodegradable “shrimp leather” comprised of by-products of the shell food industry. It uses chitosan—a carbon-neutral plastic derived from the substance from which crustaceans’ exoskeletons are made. Transformed into a thin, durable, and flexible material, chitosan is the second-most-abundant biopolymer on earth. Importantly, TômTex offers complete aesthetic versatility of its biofabric, allowing color, transparency, and opacity to be shaped according to tastes and requirements in the production process. It also lends itself to being custom-molded, embossed, and stamped to achieve a variety of finishes.
Versatility and customizability are both key features to achieving application and use at scale. TômTex is already gaining traction in various industries—not only in fashion and accessories but also in home furnishings and luxury cars, where distinctive features are key.
Aesthetics as the selling point
Critically, we’re seeing a pivot in perceptions of biofabricated materials. Eco-products were once considered inferior to “traditional” ones. But branding and product innovation have since made the offering more premium to reassure skeptical consumers. Biomaterial innovation will also increasingly prove its worth in terms of durability, versatility, and (in certain cases) luxuriousness too. Watch this space—conservative notions of function and beauty will be challenged and redefined as biofabrication comes into its own.
MycoWorks is one such startup reaching commercial scale. Last year, the company raised $125 million to launch the world’s first Fine Mycelium production plant. A pioneer in mushroom leather, MycoWorks has formulated a biomaterial so exquisite that Hermès—famed for luxurious leather accessories—used it to create a $4,200 handbag.
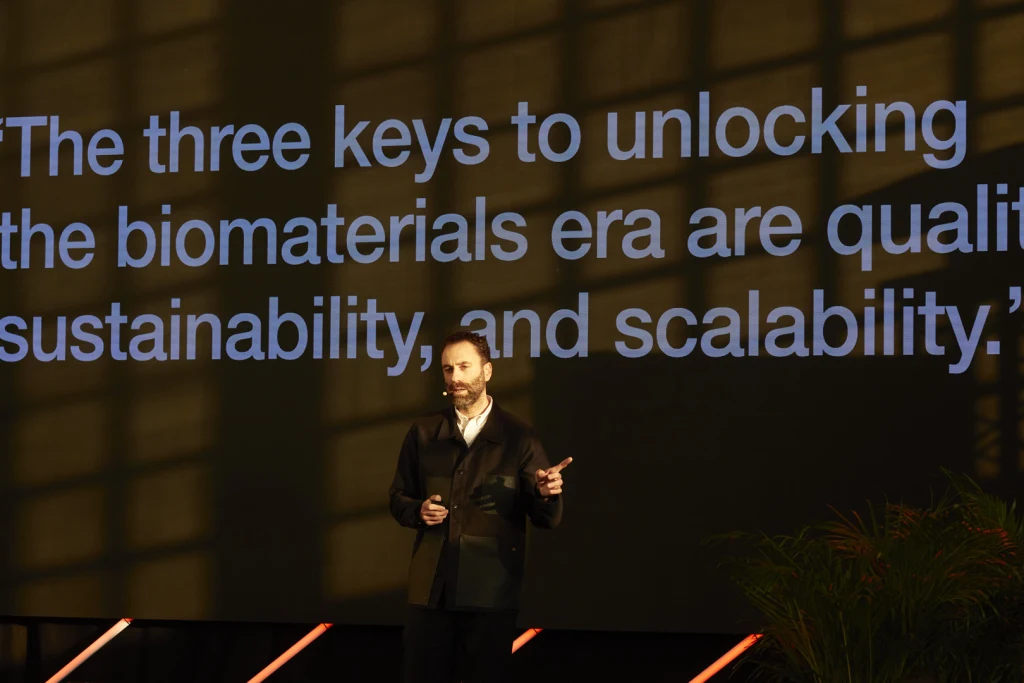
That such a fine material can be produced from what Matt Scullin, CEO of MycoWorks, has coined a “solid-waste recycling facility,” is quite remarkable. There’s no fuzzy, romanticized brand narrative about leather derived from pampered cows grazing on lush fields here. Reishi, MycoWorks’ flagship material is, instead, grown from biomass waste (such as sawdust), but the end result surpasses the tactility of some of the finest animal leathers—with a much lower environmental impact and at a competitive cost.
Bring in the robots
Of course, the next generation of materials can impact long-term global sustainability only if they’re made simple, affordable, and available at scale. The raw materials themselves (that is, waste or living organisms) might come at a cheaper price than other conventional materials, but it’s the labor-intensive processes of biofabrication that have prevented its market growth. Thus, automation will be fundamental to unlocking affordability.

The deployment of automated robots has cut the human labor time required to develop one tray of MycoWorks Fine Mycelium by 92%. The 1.3 human hours spent on production processes are invested solely in refining the quality of the material itself, giving it that artisanal touch. Furthermore, because Reishi—much like bread—is produced in batches (as opposed to rolls), processing is more economical and allows suppliers to have more control over the output.

Perhaps a key factor in previous biotech companies not achieving market growth is that the organizations weren’t designed with scalability in mind from the start. Colorifix (a U.K.-based bio-dye-process company) uses synthetic biology to produce, color, and fix dyes biologically, avoiding harmful chemicals while reducing water and energy use as well as overall waste. Its business model is based on the concept of drop-in solutions, which can be plugged into any existing dying system requiring no additional specialist equipment. Existing supply chains can easily adopt drop-in solutions, as they don’t require investment in entirely new plants and can operate within existing processes.
Innovating biomaterials is one thing, but creating technologies that optimize use of existing infrastructures will ensure scale.
Using waste streams as feedstock
While there’s much promise and enthusiasm around bio-innovations, it’s important to stress that biomaterials aren’t always better, or necessarily biodegradable. The environmental benefits must be reviewed on a case-by-case basis, and the importance of the feedstock in this assessment is vital. The raw material used should come from a nonpetroleum, nonchemical, nonpolluting resource and ideally from a traceable waste stream. Alternatively, it should exist in nature (in abundance), be renewable, and be extracted sustainably.
But what if we could solve two problems at once and directly use carbon emission as the feedstock for biology? At the Biofabricate Summit, carbon capture companies illustrated how the technology could be used to produce high-value materials.
Lanzatech, the biggest player in carbon capture technology, captures gas from a steel mill in China and then feeds it to microbes inside bioreactors. The by-product can then be turned into ethanol, which, in turn, evolves into polyester. California-based biomanufacturer Mango Materials takes methane from wastewater plants to formulate PHA—a biodegradable bioplastic used for packaging, films, and molded consumer goods. Japanese startup Spiber, meanwhile, uses a circular solution for transforming end-of-use textiles and agricultural waste into nutrients for microbial fermentation and the production of novel protein materials.
Such technologies encompass the principles of circularity effectively, transforming otherwise harmful and discarded waste into something that feeds biomaterials or informs its composition.
The future of biotech?
Despite the current economic challenges, the appetite for green investments shows no signs of abating.
Still, the biotech industry does not operate in a vacuum. Wider attention must be paid to address the infrastructure of recycling, including composting. One would hope that in the near future, regulation would differentiate a biodegradable plastic bag from a compostable shoe, for example, in order to optimize recycling processes.
Until then, I’ll be tracking biofabrication’s growing and significant role in facilitating cleaner, circular manufacturing processes.
ABOUT THE AUTHOR
Fast Company
(7)
Report Post