May 02, 2024
Why this 4th-generation woodworker built 30 machines to automate his job
Ros Broughton built custom wordworking machines to help him make craftsman-quality furniture more affordable.
Ros Broughton is a fourth-generation woodworker. For the first 15 years of his career, he mostly focused on high-end cabinetry and custom furniture. Then he decided to move away from ultra-luxury work and produce more affordable furniture. After starting his new company, Fyrn, he found himself in a bit of a pickle: The first chair he designed was such a big hit that orders were rolling in faster than he could make them. So fast that Broughton found himself wondering: “How are we going to make this next order?”
Broughton’s conundrum is a good problem to have, but it highlights an industry-wide problem: Handmade furniture—especially made from local materials—isn’t easy to scale. At least not affordably, or in a timely fashion. There are only so many joineries a pair of hands can make in a day. The slow process, high labor costs, and wait times all have a drag on small businesses that want to grow.
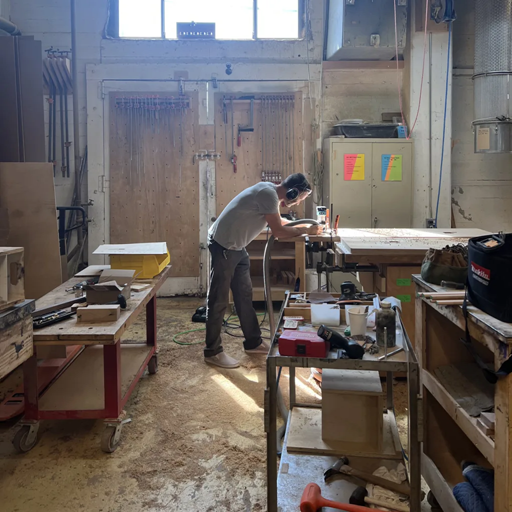
To solve this issue, Broughton decided to outsource some of his work to machines. He developed a series of “green machines,” which he and his team use to perform specialized tasks like making precise cuts on a piece of timber, or drilling a hole in a specific location. The point of these machines (which are called “green” because they are painted green) is not to replace the human hand, but instead to help Broughton make a quality piece of furniture as affordably as possible. Or as Fyrn’s cofounder, David Charne, puts it: “to bring the level of custom quality craftsmanship to a product that is scalable.”
Whether you find Fyrn’s chairs affordable will largely depend on your familiarity with custom furniture pricing, and your ability to dissociate yourself from the price tags you’re used to seeing from the likes of Wayfair and West Elm. A Fyrn chair starts at $500, while dining tables from the studio’s latest collection, Keyhole, start at $5,400. Both were made with the help of green machines.
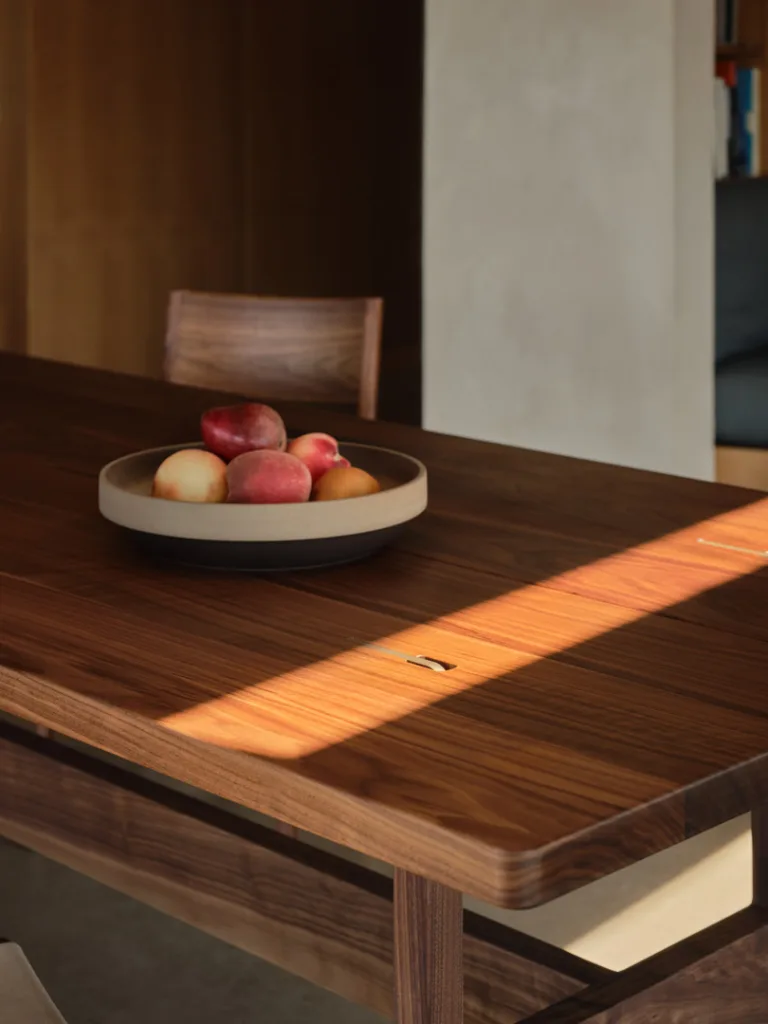
Making a green machine
Since 2014, Broughton has designed and built 30 green machines from scratch, often rushing to make them as orders rolled in. Some machines can shape the end of a piece of wood in a particular way. Others can perform multiple consecutive tasks, including cutting one side of the timber, drilling a hole, cutting the other side of the timber, and scoring it.
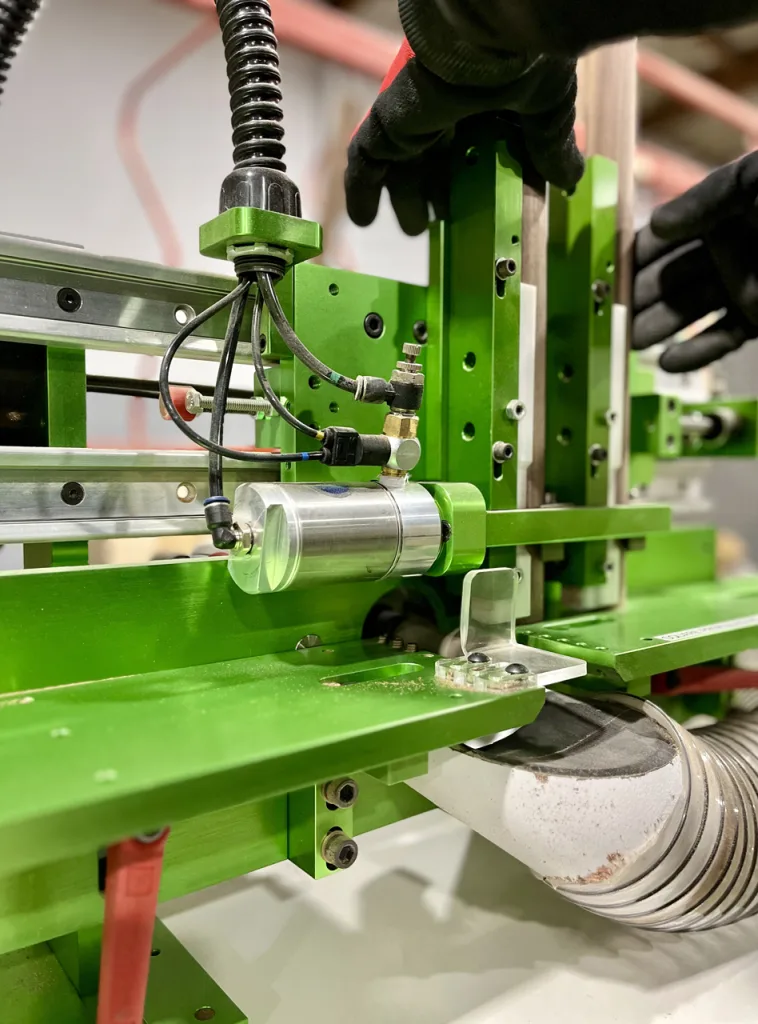
The first green machine Broughton built made precise cuts on the ends of a frame so they could attach to a metal bracket he had also designed. By hand, that cut would take around an hour. With a machine, it takes 8 seconds. Broughton estimates that it’s about 20 to 30 times faster to build a chair using the green machines than it is to build one by hand. (The machines were starting to take up so much space that, in 2022, the company had to move its production facility from an artists’ loft building in San Francisco’s Mission neighborhood, to Sparks, NV.)
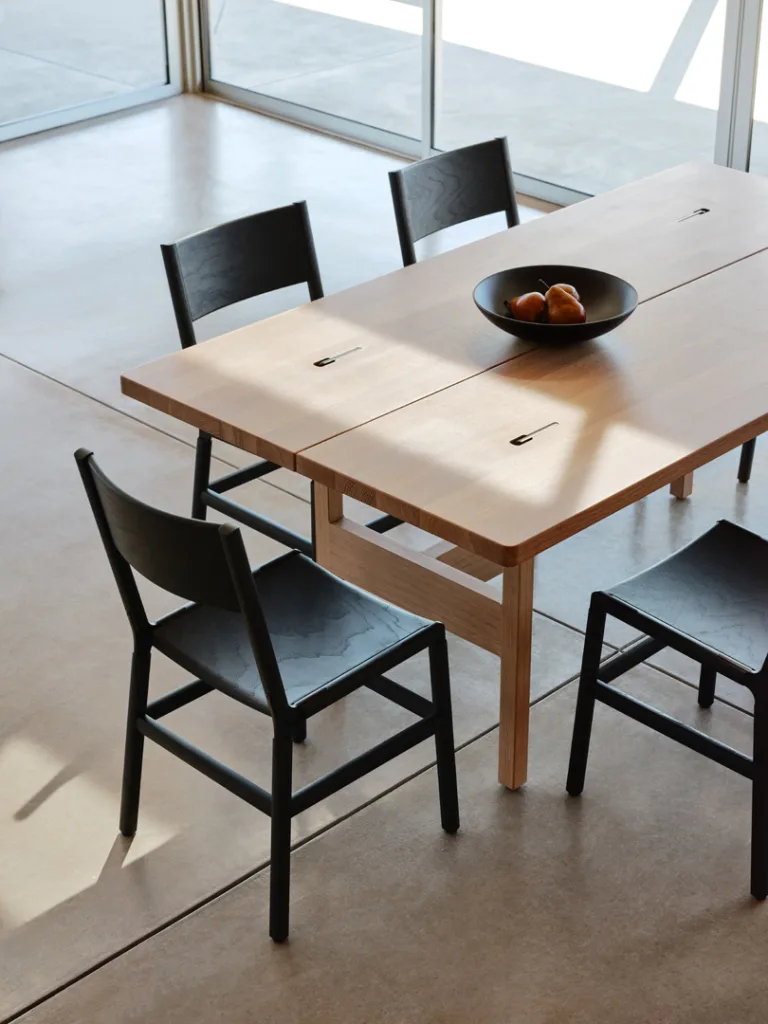
The green machines have helped Broughton increase efficiency across Fyrn’s manufacturing process. Underpinning that process is a proprietary design system called Stemn, which Broughton designed as a set of joints and brackets that are interchangeable across various models and furniture collections. The system means that a Fyrn table and a Fyrn chair have overlapping components, which makes the company more nimble. If an order falls through mid-way, for example, they can reallocate the parts to another order. This helps with inventory management, as well. “The same components can be used across multiple products, which allows us to stock a lot less inventory and be very lean in that capacity,” says Charne.
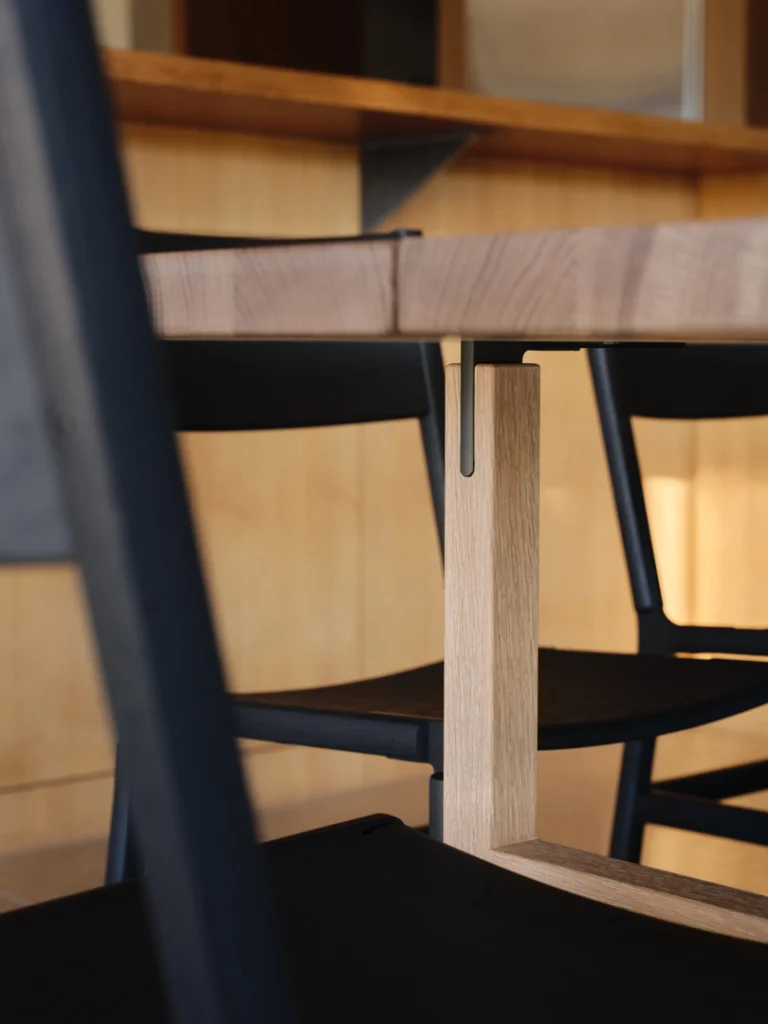
You might find it perplexing that Broughton, who has spent years honing his craft as a woodworker, would chose to delegate some of his work to an army of machines. But when asked if he worries that he’s building machines that could render his own skills obsolete, Broughton’s response echos that of many designers who are grappling with their role in the age of AI: “I feel like my skills as a craftsman have massively expanded and improved since I took on this project because it’s forced me to learn a lot of new things that aren’t just how to chisel and cut a piece of wood,” he says. “My skills are more honed than they’ve ever been.”
ABOUT THE AUTHOR
(11)
Report Post